Neues von der Hostel Baustelle: Die hochgelegte Bodenplatte
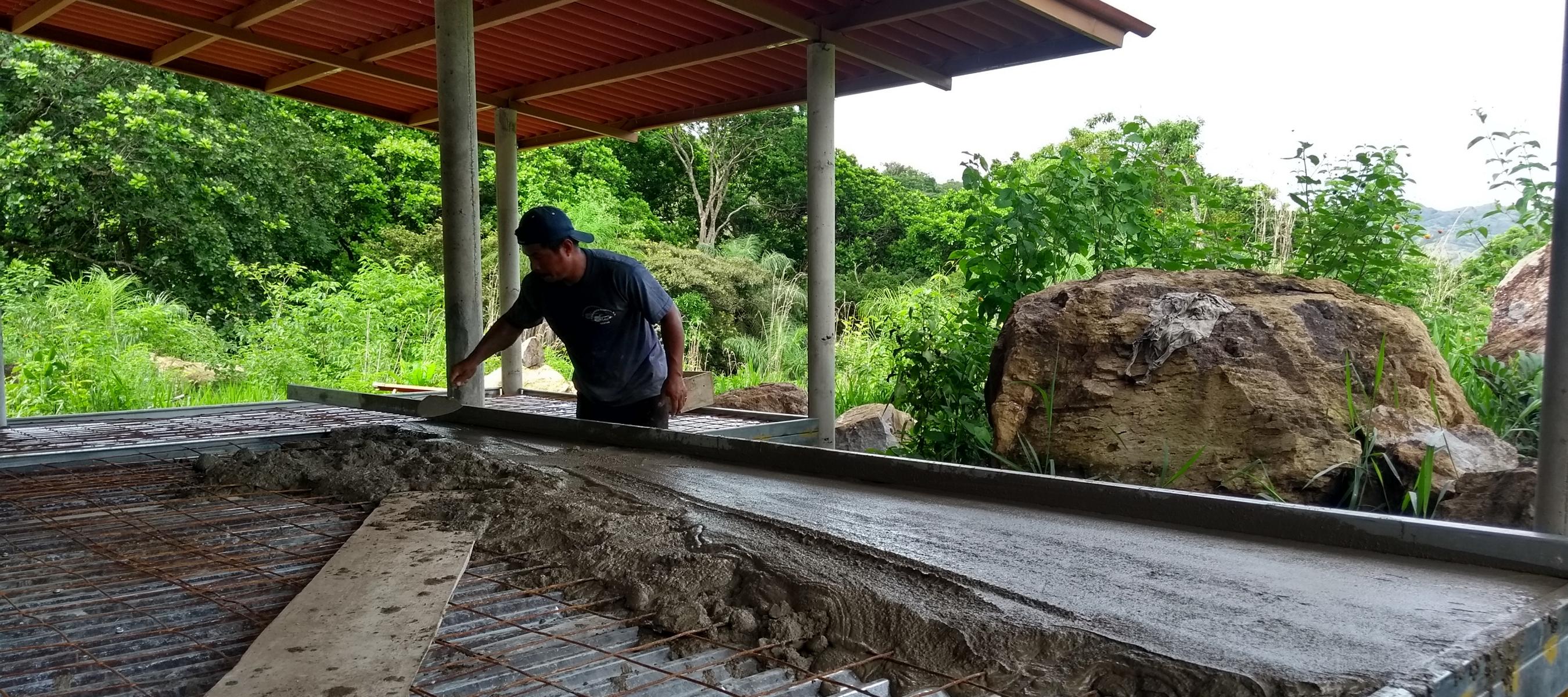
Es scheint die Sonne auf der Finca und das Wetter ist für diese Jahreszeit trotz gelegentlicher Niederschläge, eigentlich immer noch viel zu trocken. Das Grünzeug wächst trotzdem wie verrückt und auch die Frösche quaken sich die Seele aus dem Leib. Auf unseren Baustellen ist uns ein eher trockenes Wetter auch nur recht.
Mit riesen Schritten voran geht es bei unserem Küchengebäude, wo wir ja erst kürzlich das große Schleppdach fertiggestellt haben. Und in dem Moment als die ehemalige Wiese trocken und schattig war, ging es auch schon an den nächsten Arbeitsschritt. Na klar, eine Bodenplatte wäre auch hier wünschenswert. Das war jedoch leichter gesagt als getan. Um euch nochmal einen besseren Eindruck unserer Pläne zu vermitteln, habe ich weiter unten ein 3D-Model eingefügt.
Bei der Planung des Schleppdachs war die spätere Bodenhöhe natürlich kritisch, da wir auf keinen Fall die schöne Aussicht verbauen wollten. Und da wir hier wieder mal auf ziemlich unebenem Terrain bauen, wo auch der ein oder andere Fels im Weg liegt, entschieden wir uns erneut dazu, den Betonboden nicht direkt auf den Grund, sondern auf einen erhöhten Stahlrahmen zu gießen.
Die Vorteile einer solchen Konstruktion sind vielfältig. Bei den starken Regenfällen hier ist es generell immer ratsam, die Bodenplatte etwas erhöht anzulegen. Neben dem Wasser hält man so auch zumindest einen Teil der Krabbelviecher zurück. Bei normaler Bauweise würde man ein Streifenfundament anlegen, auf die gewünschte Höhe aufmauern und den entstandenen Hohlraum mit Erde füllen.
Um uns einige Kubikmeter schaufelarbeiten zu ersparen und den Bau der Bodenplatte außerdem schnellstmöglich voranzutreiben, war das Stahlfundament wie gesagt die bessere Wahl. Und da Sven eh nichts lieber tut als zu schweißen, war es ziemlich schnell entschieden. Also sind wir erstmal mit dem Hänger nach Santiago gefahren, um knappe 200 Meter Stahlprofile sowie 10kg Schweißstäbe zu besorgen.
Ganze Tage verbrachte Sven dann in der Werkstatt, wo er aus den einfachen C-Profilen doppelte und dadurch viel stärker belastbare Profile, zusammenschweißte. Und bevor wir dann die ersten Stützen im Boden verankern konnten, mussten wir erst das gewünschte Höhenniveau für die spätere Platte bestimmen.
Nicht zu hoch und nicht zu niedrig sollte sie werden und nach viel messen und probieren fanden wir schließlich den kleinsten gemeinsamen Nenner. Trotz aller Kompromisse blieb ein Fels im Weg, der einfach zu hoch aus der Erde ragte. Erst mit unserem Abbruchhammer, dann mit der Flex und zu guter Letzt mit Hammer, Meisel und roher Gewalt.
Dem Stein ging es so weit an den Kragen, bis er für die Bodenplatte schließlich kein Problem mehr darstellte. Da das Gelände auf eine Seite abschüssig ist und wir am hinteren Ende nicht zu hoch rauszukommen wollten, entschieden wir uns außerdem dazu, die Bodenplatte aus zwei Teilen mit unterschiedlicher Höhe zu gestalten.
Schließlich konnten wir damit beginnen, die äußeren Ränder der Stahlrahmen zwischen den Säulen zu befestigen. Während das untere doppelte Stahlprofil als Tragwerk dient, schweißte Sven ein zusätzliches Profil darüber, welches als Schalung für den Beton fungiert. Als die Ränder erst mal fertig waren, folgten noch zahlreiche Verstrebungen in Quer- und Längsrichtung, was am Ende zu einer gewaltigen, schachbrettartigen Stahlkonstruktion führte.
Als nächstes mussten hunderte Schweißstellen erst mit der Drahtbürste gereinigt und anschließend mit Metallschutzfarbe eingestrichen werden. Erst dann konnten wir damit beginnen, das dünne verzinkte Wellblech, welches wir für die untere Schalung vorgesehen hatten, zu montieren. Zurechtgeschnitten und festgemacht war es schnell, doch das Material erwies sich als hauchdünn und es war fragwürdig, ob es der Belastung durch den Beton standhalten würde.
Egal, versuchen wollten wir es so oder so. Die Baustelle war nun soweit vorbereitet, doch etwas ganz Entscheidendes fehlte noch: Sand! Sven hat eben mal durchgerechnet und ist auf die unglaubliche Menge von 60 Tonnen bzw. rund 40m³ Sand gekommen, den wir mittlerweile schon vom Fluss angekarrt haben. Der Hänger hat sich dabei als sehr nützlich erwiesen, doch auf- bzw. abschaufeln mussten wir das alles natürlich von Hand mit der Schaufel. Krass!
So verbrachten Sven und Isais einen weiteren Tag am Fluss und karrten einen ganzen Berg Sand an. Am nächsten Tag als wirklich alles bereitstand, war es an der Zeit die Betonmischmaschine anzuwerfen. Und da passierte es. Das Seil des Starters, welches wir schon mehrmals getauscht und repariert hatten, riss erneut.
Und wie es aussah war die Spule nun ganz am Arsch, was den dicken Betonmischer ziemlich alt aussehen ließ. Ein weiterer Tag war verloren, doch anstatt den Kopf in den Sand zu stecken, erfand Sven kurzerhand eine Lösung für das Problem. Er schweißte einen Adapter welcher auf die Kurbelwelle des Motors passte, und auf der anderen Seite mit dem Akkuschrauber gedreht werden konnte.
Anstatt an der blöden Kordel zu ziehen, werden wir unseren Betonmischer von nun an einfach mit dem Akkubohrer starten. Sehr geil! Am nächsten Tag funktioniert es dann auch prächtig und die beiden Schwerarbeiter konnten damit beginnen, den ersten Teil der Bodenplatte zu gießen. Nach rekordverdächtigen 4 Stunden waren sie mit dem größten Teil bereits fertig.
Wie üblich nach solchen kräftezehrenden Arbeiten, gab ich dann eine Runde Bier aus. An diesem Tag wurde dann nicht mehr viel gearbeitet, was aber auch kein Schaden war. Die zweite Platte steht bevor und damit auch nochmal ein Ausflug zum Fluss, um neuen Sand zu holen.
Doch im nächsten Bericht werde ich euch erstmal davon berichten, was ich eigentlich die ganze Zeit gemacht habe. Bis dann!